My First O.S.S. Attempt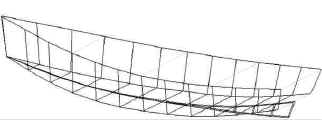 |
This design of June of 1999 was my first attempt at designing a one sheet
boat with more capacity (holding an adult and a
kid) than Herb's OSS (one sheet skiff) My idea was to make the transom out of 1 x 12 pine
to allow all the ply to go to the hull. That approach carried over well into Summer
Breeze, and my One Sheet Pram
OSS. This one looks very "salty" but has inadequate freeboard.
None the less, this page shows some of what I learned about modeling
that can be applied to any boat. |
Model making - Quick and Easy
Even with all the modern 3D modeling available from the
various boat design software out there - the time comes when there is no
substitute for holding a model in your hand and studying it from every angle.
What follows are some simple tricks to making the transition from two
dimensions to three a bit smoother. I start with a cardstock model and then go
to a balsa wood one.
The sample boat I'm modeling here is one I'm exploring
based on the flat iron skiff, but made of a single sheet of 4'x8' plywood. I'm
making the transom of 1"x12" pine to maximize the displacement
available from a single sheet of ply. I designed this onGregg Carlson's
free hulls software. (Let
the page load, the program is at the bottom.) Gavin Atkins has a great tutorial
for it here. Click on thumbnails to see
larger image, then use your back button to return.
Here
are the views. The water line is at 300lb displacement.
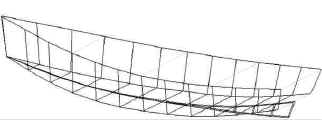
Here's
a perspective view of it.
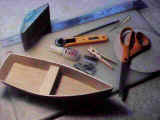 A
few simple tools and a little patience can yield some satisfying results. Most
of what you'll use you probably already have around the house. Sissors,
clothes pins, sandpaper, ruler (straight edge) single edged razor blade,
pencile and assorted glues.
The only not so common item is a circular razor wheel made
for cutting fabric. It works great on paper and balsa wood as well, and sort
of simulates cutting out your parts with a circular saw.
How you get to your developed panels is up to you. You can
play directly with cardstock and sissors if you like. Than transfer that to
graph paper to create offsets for lofting your full sized boat. If you already
have some offsets you can draw them to scale on graph paper and make xerox
copies of them, or enter them into a CAD program like TurboCad, and connect
the dots with a spline curve. Or if you are using hulls software as I was in
this example you can do a screen save on the nesting portion. Open the ply
layout image in any graphic view program and print onto card stock. If you
don't have any cardstock handy, file folders are a good weight for the paper
models as well.
Here's
the screen shot I did for my One Sheet Flat Iron Skiff.
Cut out your parts and tape them together.
If this inspires you to tweak your design, do so and make another paper model
until you like what you see. Now use the paper pieces as patterns to cut out
your balsa wood. Trace them onto your balsa wood sheet and cut them out with a
razor blade or wheel. Some like to use a scale of 3/4 inch to the foot as this
allows 1/16" to equal an inch. I tend to just print my patterns as large
as I can fit onto the card stock I have, and leave it at that. The wood pieces
become a kind of kit. I like to simulate the construction technique if
possible. Hot melt glue simulates epoxy fillets in stitch and glue. Otherwise
I try to make all wood parts that the full size boat will require. Much can be
learned about assembly this way, when changes are easier to make, and less
costly.
In
spite of what I just said, rather than make the stem post, I cheated and used
hot melt, even though this boat is not destined to be a stitch and glue. I
taped the ends of the sides together and then while holding them at the
designed angle, I applied the hot melt.
Here
are the main parts of the boat, sides transom and middle frame.
A
rubber band and a bamboo skewer make a fine "Spanish windless."
Notice I chose to use a solid frame instead of the stick and gusset one, for
the bending stage.
Here
are the sides and transom glued together.
Here
the gunwales are being glued on. (On the full size boat, slices of PVC
pipe work wonderfully as clamps.)
The
chine logs go on next.
Sanding
chine logs.
Checking
for fairness before gluing bottom.
The
bottom is cut oversized prepared to glue to the hull frame.
Bottom
is sanded flush and skeg attached.
Seats
and deck are glued in place.
I ultimately decided it would be easier to design a 2 sheet skiff that could have about 400 lb
capacity with only slightly more effort than the OSS. Mike Goodwin's creation also inspired
my doodling. Check out his article
at the Duckworks Mag.
|